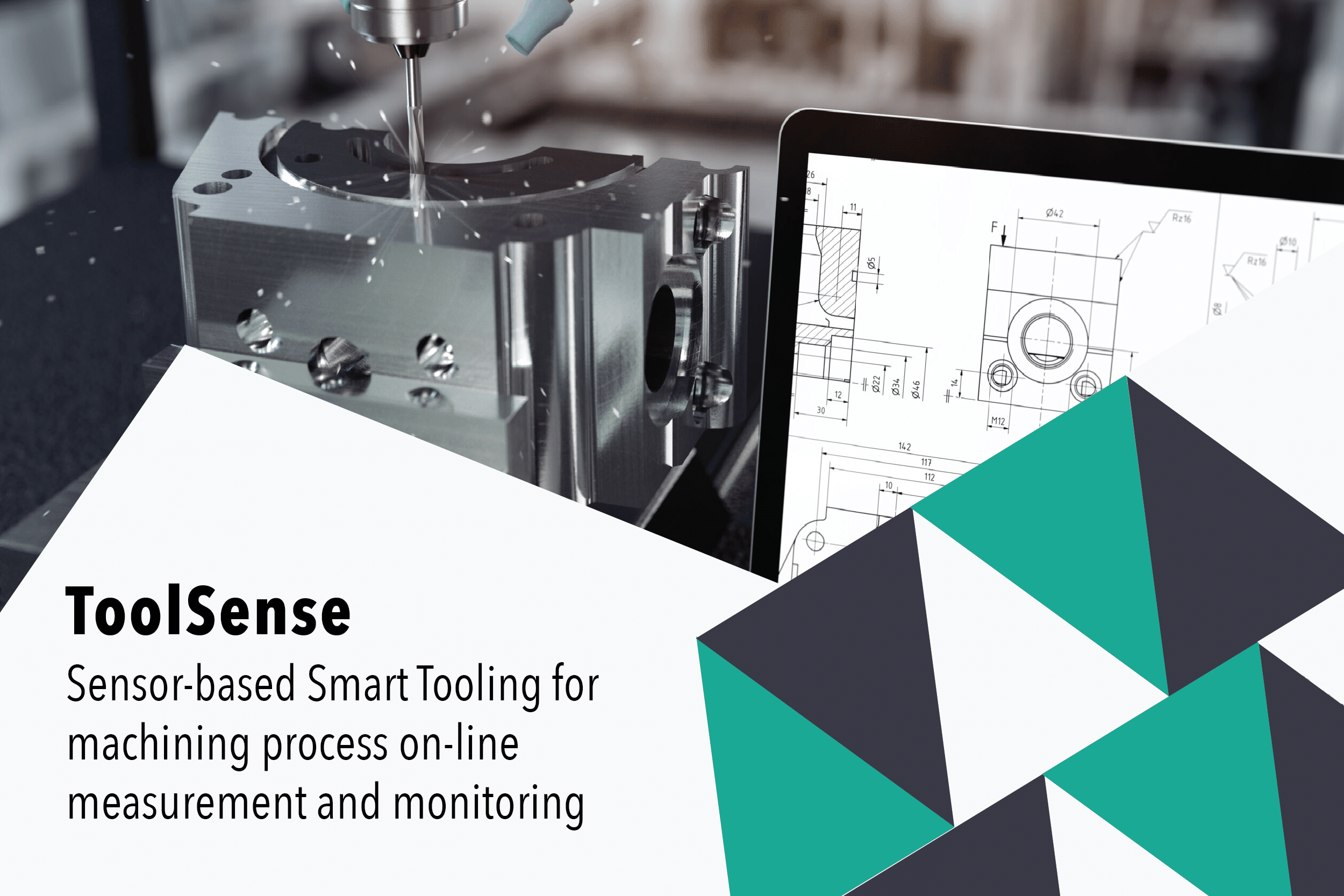
ToolSense – Smart Cutting Tool Technology
Rainhouse, has joined efforts with the National Research Council – Aerospace Manufacturing Technologies Center (NRC-AMTC), and key members of the Swedish manufacturing industry to work on the ToolSense project.
The ToolSense project aims to develop smart tools for metal and tool cutting. The smart tool obtains information and feedback from a thin-film and nano-sized semiconductor device located on the tool and platform. Our objective is to develop, upscale, and commercialize this Smart Cutting Tool. It can be implemented in the manufacturing of advanced aeronautic and hydraulic components.
This multi-sensory Smart Tool will measure and monitor vibration, force, temperature, and acoustic emission on Computer Numerical Control (CNC) Machines. It will be helpful in many industries including: automotive, aerospace and defence, power and energy, construction equipment, and industrial sectors.
BENEFITS OF THIS NEW TECHNOLOGY
Integrated data collected through sensors on CNC machines will open the CNC market to new commercial tools and applications that create a supportive infrastructure, enabling viable products for use in industry and academia.
Continuous data feedback will streamline machining operations to create improved process control, leading to cost savings, reducing waste, and minimizing re-tooling benefiting the machining industry.
This new technology will also aid academia and scientific pursuits with access to high-resolution time and position data from the sensors. This data will allow significant scientific progress, advanced research and development capabilities for businesses.
RAINHOUSE’S CONTRIBUTION
Rainhouse will use a vibration sensor to identify harmful frequencies during the machining process in the ToolSense project. Furthermore, we will provide an electronic hardware platform to interpret data for the user. The vibration sensor will effectively measure frequencies that could be harmful to CNC machines. The sensor will transmit the data to the electronic hardware platform.
We will need to create a Vibration Measurement Module, a Multi-sensor Fusion Module, and Stationary and Rotating tools to complete the project.
- The component to measure vibration is currently characterized and benchmarked, ready to be optimized and validated.
- The Multi-sensor Fusion Module will integrate high-speed signal processing, wireless data transmission, power supply, and receiving qualities.
- The stationary and rotating tools are currently in the final stages of development. After completing the development stage, our Consortium Partners from SECO will begin the manufacturing and delivery process.
MOVING FORWARD
Upon completion of the Vibration Measurement Module (VMM), we will have a “machine-ready test platform” for both electronics and firmware. Integrating our hardware solution with the stationary and rotating tools provided by SECO will come after the VMM and Multi-Sensor Fusion Module (MFM) are working together.