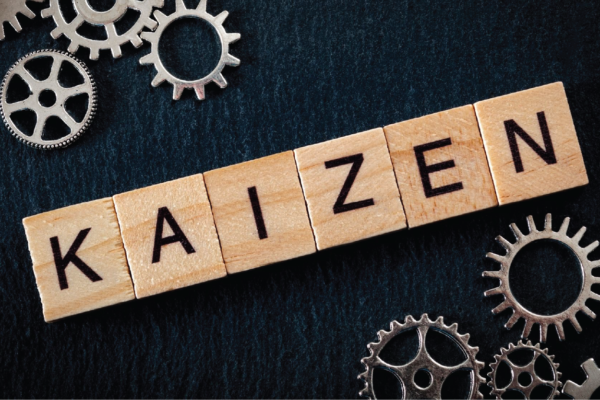
KAIZEN – Rainhouse’s Continuous Improvement
KAIZEN: Japanese for “change for the better” or “continuous improvement”, and also known as Lean Manufacturing. Kaizen is a strategy to reduce or eliminate non-value-adding activities in a process. We evaluate activities using three main Kaizen/Lean concepts: identifying and eliminating waste, improving workspace organization and efficiency, and implementing continuous improvement. By applying these concepts at all levels, everyone can collaborate and achieve regular progressive improvements in the manufacturing process.
The 8 Wastes
We identify and eliminate waste by applying the 8 Wastes principles. The 8 Wastes allow us to define what process or area we aim to improve or eliminate.
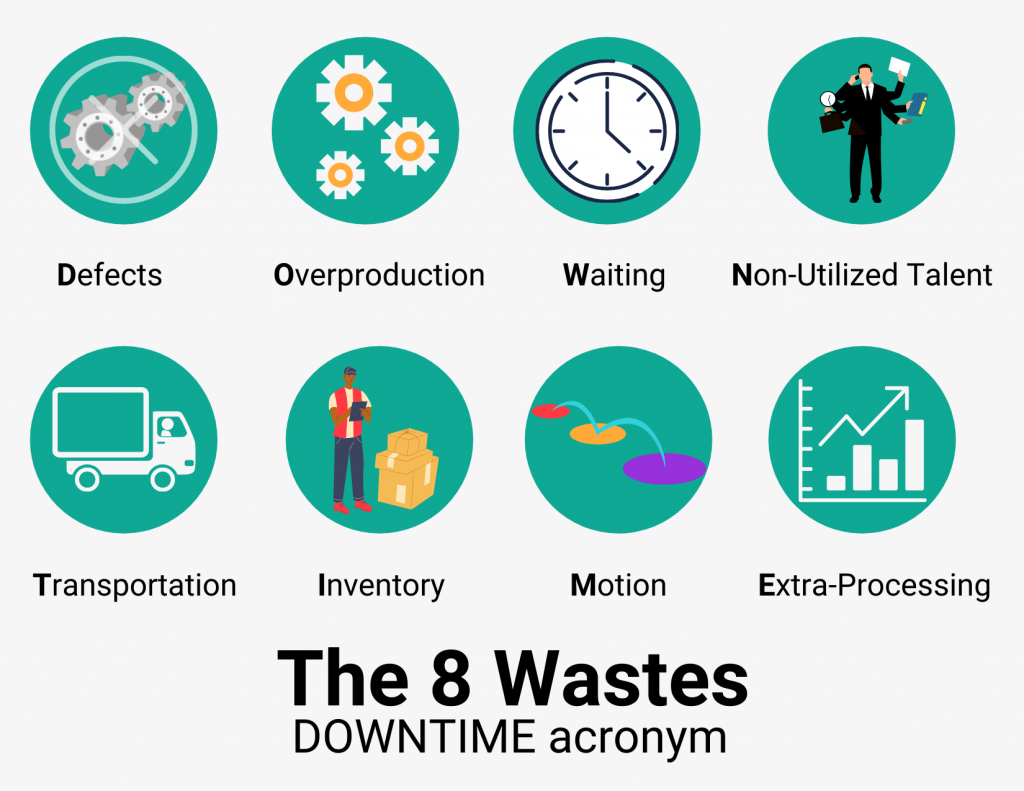
- Defects: waste from product or services that failed to meet clients’ expectations
- Overproduction: Waste from making more product than on demand
- Waiting: Waste from time spent waiting for the next step to occur
- Non-utilized talent: Waste from underutilizing people’s talents, skills, and knowledge.
- Transportation: Waste from time, resources, and cost from moving unnecessary products and materials
- Inventory: Waste from excess product and materials that are not processed
- Motion: Waste time and effort from people’s unnecessary movements
- Extra-processing: Waste from excess work or quality required.
The 5s System
The second concept in the Kaizen method involves improving workspace process organization and efficiency. This concept explains how to physically eliminate the eight wastes. The 5 S system is the process of developing solutions to reduce waste, optimize productivity using visual cues, and have consistent operational results. The 5 S system includes Sort, Set in order, Shine, Standardize and Sustain.
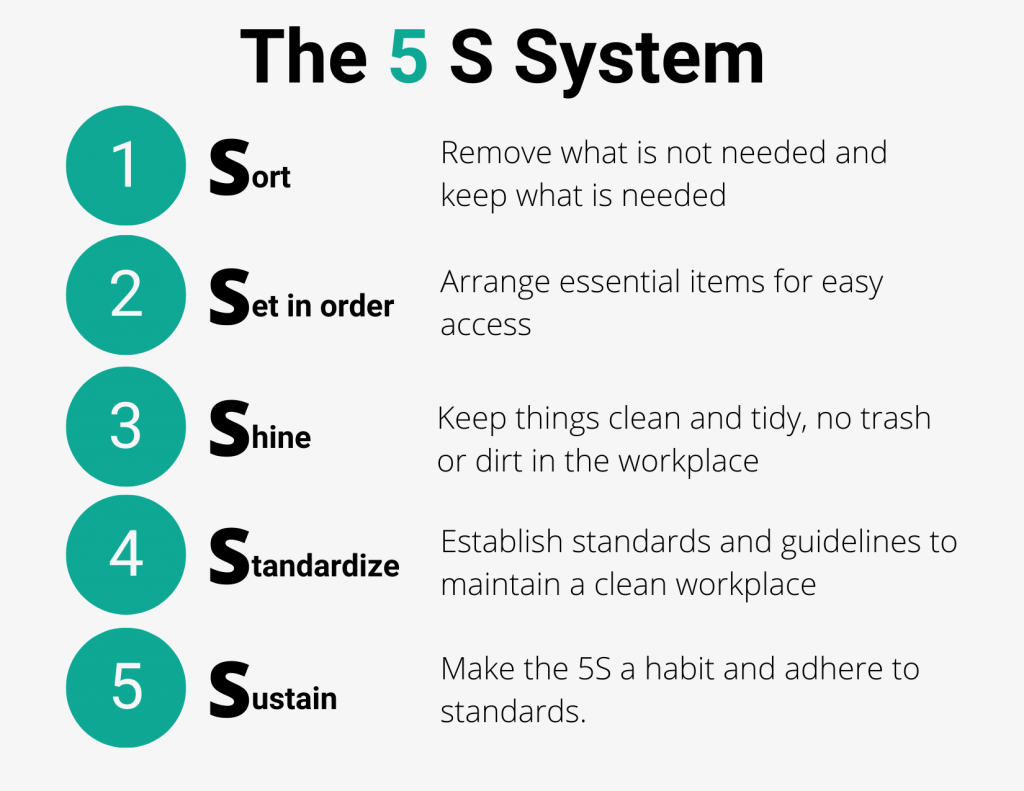
With the Kaizen approach, there is always something new to improve or optimize. The idea is never to think of an area or process as complete but instead look for ways to improve them further.
Kaizen Lean Improvements
Rainhouse is committed to a Lean work environment that is enjoyable for its employees and allows them to have higher productivity. This perspective allows for greater efficiency and enables employees to get more done. By implementing Kaizen principles, Rainhouse has seen greater customer satisfaction and is ensuring the company’s long-term viability.
Since late 2020, all Rainhouse employees have dedicated the first 15 minutes of their workday to thinking Lean first. This practice has allowed all employees to improve their work areas, the company as a whole, where they can see immediate effects and witness valuable time-saving solutions.
One of the improvements made in the office area to date includes relocating the printer. This allows employees faster access to their print materials. This small change reduced the number of steps to the printer in half, enabling the users to save time. Over the course of one year, this small change will save a total of 1560 steps and approximately 25 minutes during the year.
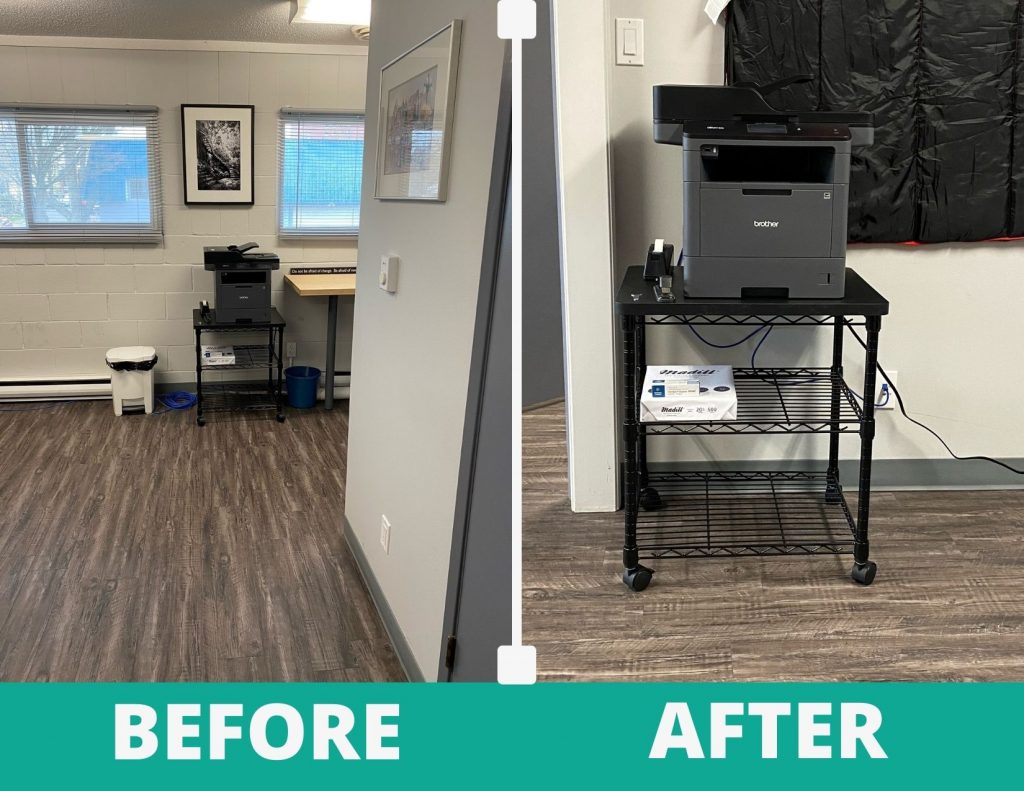
Another example of the improvements made at Rainhouse is the organizing and rearranging of tools in drawers by utilizing foam inserts, known as Kaizen foam, to compartmentalize where each tool should go. This change will make it easier to find the exact tool needed and facilitate better organization in the workspace. Each tool now has its specific storage space within the drawers.

At Rainhouse, we continue to make a conscious effort to optimize processes, increase efficiency, and make it easier for our team to do what they do best, make innovative ideas a reality.